How to Strike the Perfect Balance for Inventory Optimization?
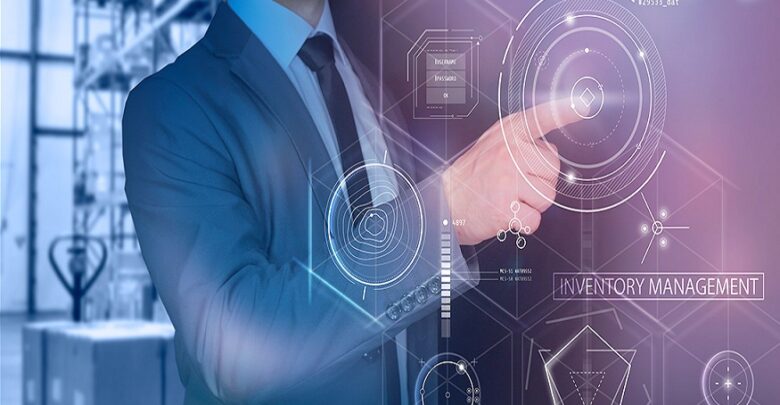
Inventory optimization is the process of figuring out the ideal stock levels to save expenses and increase a company’s profitability. It entails weighing the expenses of stock-outs and missed sales as a result of insufficient stock against the costs of maintaining inventory.
Finding the ideal balance between too much inventory, which uses up capital and results in storage and handling expenses, and too little inventory, which may result in stock-outs and lost sales, is the aim of inventory planning.
Effectively managing inventory levels involves utilizing a range of methodologies, such as analyzing demand forecasts, employing inventory planning systems, and utilizing statistical analysis. When calculating the ideal levels of inventory, businesses also take lead time, safety stock, reorder point, and carrying expenses into account. Businesses can enhance customer service, raise profits, cut costs, and better manage their working capital by optimizing their inventory.
Importance of Inventory Optimization
The capacity of inventory optimization to help firms stay competitive by lowering costs, satisfying consumer expectations, and maximizing profits is crucial in the current business environment. Businesses may stay ahead of the curve and thrive in a market that is becoming more complex and competitive by employing efficientinventory planning tactics.
- Optimize Inventory to Meet Customer Demands: Businesses may guarantee that the correct products are available when customers need them by precisely anticipating customer demand and optimizing inventory levels.
- Cost Savings: Inventory replenishment costs can be reduced with the use of inventory optimization. Businesses can save carrying expenses, such as storage, insurance, and obsolescence, by avoiding having an excessive amount of inventory.
- Boost Profitability: A company’s profitability is directly impacted by efficientinventory plannning. Businesses can save inventory holding costs and lower the risk of obsolescence by matching inventory levels to customer demand.
- Be Competitive: Keeping one’s competitiveness in the market requires careful consideration of inventory planning. Businesses can react rapidly to market shifts and customer demands by having the correct items available when customers need them. Customers will be happier as a result, and firms will have a competitive advantage over rivals.
Businesses can establish a balance between customer pleasure and cost minimization by controlling inventory levels correctly, resulting in long-term profitability and sustainable growth.
Factors to Consider in Inventory Optimization
Making informed judgments about inventory planning requires taking into account a number of issues, including balancing the expenses of holding goods with the risks of stock-outs and lost sales.
- Demand Forecasting: For effective inventory replenishment, accurate demand forecasting is essential. This entails forecasting product demand based on historical data and trends as well as taking into account elements like seasonality, marketing campaigns, and shifting market conditions.
- Lead Time: The lead time is the period of time between when a company receives an order from a supplier and when it becomes available for sale. This is a crucial aspect of inventory optimization to take into account because it can affect the quantity of inventory a company has to keep on hand to meet client demand.
- Safety Stock: Extra inventory is kept on hand by a company as a precaution against stock-outs. This is a crucial aspect ofinventory planning to take into account because it can affect the quantity of inventory a company has to keep on hand to meet client demand.
- Holding Costs: Holding costs, such as storage and handling fees, are expenses incurred when managing and holding inventories. In order to reduce the overall cost of inventory, these charges must be taken into account during inventory optimization.
- Ordering Costs: While we talk about ordering costs, we’re talking about the expenses incurred while placing an order with a supplier, like shipping and handling fees. In order to reduce the overall cost of inventory, these charges must be taken into account during inventory planning.
- Stock-Out Costs: Stock-Out Costs are the expenses related to stock-outs, such as lost sales and reputational harm to a company. In order to reduce the overall cost of inventory, these charges must be taken into account during inventory optimization.
- Seasonality: To make sure a company has the proper products in stock at the right time, inventory optimization must take seasonality into account as a factor that may affect demand for particular products.
Making informed decisions aboutinventory planning requires taking into account a number of criteria while optimizing inventories. Businesses can reduce their overall cost of inventory and increase customer satisfaction and profitability by taking into account variables including demand forecasts, lead time, safety stock, holding costs, ordering costs, stock-out costs, and seasonality.
Techniques for Inventory Optimization
The reorder point approach, EOQ model, MRP, JIT inventory management, Kanban system, ABC analysis, and multi-echelon inventory optimization are some of the methods that can be utilized for inventory optimization. By implementing these strategies, businesses can optimize their inventory management and achieve multiple benefits. These include reducing overall inventory costs, improving customer satisfaction, and ultimately increasing profitability.
Several popular methods can be applied for inventory optimization, including:
- Reorder Point Method: In order to prevent stock-outs, a company must specify a certain moment at which it must restock inventory. This is determined using lead time, safety stock, and demand forecasting.
- Economic Order Quantity (EOQ) Model: The Economic Order Quantity (EOQ) model is a mathematical method used to calculate the minimum overall cost of inventory, which includes holding costs and ordering costs.
- ABC Analysis: By classifying inventory into categories according to its significance to a business, ABC analysis is a categorization approach used to prioritize inventory management operations.
Using Technology for Inventory Optimization
Inventory planning software helps businesses optimize their inventory levels by providing real-time data on sales, demand, and inventory levels. It also includes features for forecasting demand and calculating optimal inventory levels. To further enhance demand forecasting and inventory planning, AI and ML technologies can analyze various data sources such as sales data, customer behavior, and supply chain data.
About the Company
RephraseFountain9 has developed a revolutionaryinventory planningtool called Kronoscope that utilizes advanced AI technology. With this tool, businesses gain the ability to accurately forecast demand for each individual SKU item. The result is improved profitability and enhanced customer service capabilities.
Kronoscope’s advanced features include demand sensing and a price engine that takes into account historical sales trends, seasonal patterns, holidays, markdown events, and pricing fluctuations. This valuable information is utilized by the software to accurately forecast inventory needs and analyze pricing strategies. By combining anticipated demand with supply-side data, businesses can select the best suppliers and determine the proper inventory replenishmentnumbers, helping them avoid stockouts and reduce inventory waste. With Kronoscope, businesses can arrange their stocks optimally, providing them a competitive edge.