What advantages exist from 3D printing plastic?
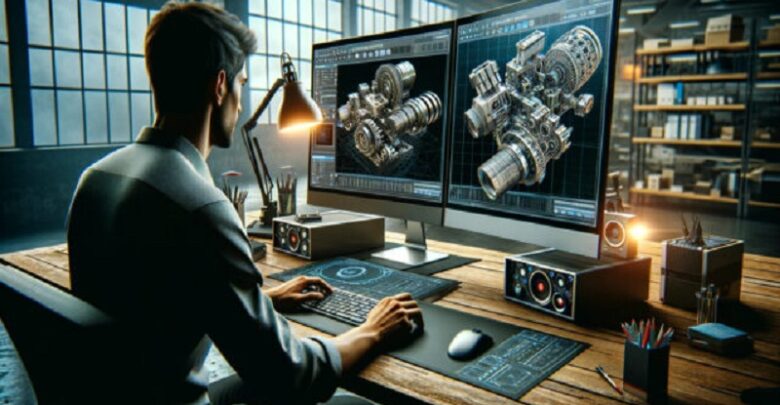
3D printing has revolutionized design and manufacture for many different industries. With this creative technology, digital models may be created in three dimensions, therefore providing unheard-of efficiency and versatility. Among the 3D printing materials, plastic is among the most flexible and often used ones. From cost-effectiveness to possible customizing, 3D printing plastic offers several benefits. The several advantages of plastic 3D printing as well as its influence on several industries are investigated in this post.
Economically Reasoned Manufacturing
Particularly for small-scale manufacturing or prototypes, 3D printing plastic offers one of the main benefits: its affordability. Conventional manufacturing techniques can call for large upfront outlays in tools, molds, and machines. On the other hand, 3D printing makes many of these expenses obsolete, which appeals to both companies and consumers equally.
The starting setup expenses of plastic 3D printing are modest. The primary costs after the 3D printer is purchased are just for plastic filament and energy. Small firms and startups may compete with bigger enterprises by making their components and goods without using costly production tools because of this low entrance barrier.
Furthermore, 3D printing plastic allows on-demand manufacturing, therefore lowering the necessity for storage space and big stocks. Significant cost reductions in inventory control and transportation might result from this just-in-time production method.
Fast Prototyping and Iteration
Rapid prototype creation and iterative design iteration are two other major benefits of 3D printing plastic. Usually needing weeks or even months to create a single prototype, traditional prototyping techniques may be costly and time-consuming. Engineers and designers can produce actual models of their ideas in a few hours with 3D printing.
Fast design validation and testing made possible by rapid prototyping enable this designer to quickly create changes to their digital models and print fresh copies, therefore hastening the cycle of product creation. Faster iterative design improvement results in improved end goods and shortened time-to-market.
In sectors such as automotive, aerospace, and consumer goods where product development cycles are essential to preserving a competitive edge, the speed of plastic 3D printing is very helpful.
Modification and Personalization
Plastic 3D printing has unmatched chances for personalizing and adaptation. Unlike conventional manufacturing techniques, which may depend on standardized molds and equipment, 3D printing lets one create original, one-of-a-kind products without further expenses.
Applications for this customizing potential abound, including medicine, where 3D-printed prostheses and orthotics may be customized to fit unique patient demands. Custom-fit glasses frames or smartphone covers are among the personalized items firms in the consumer goods market may provide, hence improving customer happiness and brand loyalty.
Easy modification of digital models also facilitates mass customization, in which items may be customized to particular consumer tastes while also preserving effective manufacturing techniques.
Simple Geometries and Design Flexibility
By enabling the construction of intricate geometries that would be difficult or impossible to attain with conventional production techniques, plastic 3D printing creates new design opportunities. Engineers and designers using these 3D printed building models flexibility can maximize components for performance instead of manufacturing.
3D-printed plastic pieces allow simple incorporation of complex interior structures including lattices and honeycomb patterns. Particularly helpful in aeronautical and automotive uses, these structures may save weight while preserving strength.
The capacity to produce intricate forms also relates to aesthetic design, enabling designers and artists to challenge form and purpose. From avant-garde furniture to complex jewelry designs, 3D printing plastic has opened the field of possibilities in product creation.
Minuted Material Waste
An additive manufacturing method, 3D printing plastic creates items layer by layer utilizing just the materials required for the finished good. Unlike subtractive manufacturing techniques like CNC machining, which produce items by cutting away extra material from a bigger block, this approach contrasts with
Because 3D printing is additive, material waste is much reduced compared to conventional production techniques. Along with economic savings, this waste decrease supports more environmentally friendly production methods.
Moreover, many varieties of plastic used in 3D printing are recyclable. Often crushed up and reworked into fresh filament, failed prints or old parts help to further cut waste and environmental effects.
Lightweight Architectures and Parts
Lightweight components and buildings made possible by plastic 3D printing may be created without sacrificing strength or use. Engineers may produce components that use fewer materials yet satisfy performance criteria by using cutting-edge design approaches such as generative design and topology optimization.
In sectors like aircraft and automotive, where weight reduction immediately results in enhanced fuel efficiency and performance, the capacity to create lightweight components is very significant. Many uses for 3D printed plastic parts allow heavier metal components to be replaced, therefore lowering total weight in vehicles and airplanes.
Apart from mobility, lightweight 3D-printed plastic components find uses in portable electronics, sports equipment, and medical tools where low weight improves user comfort and functionality.
Functional Prototypes and End-User Parts
Although 3D printing was first mostly used for visual prototypes, developments in materials and printing technology have extended its possibilities to incorporate functional prototypes and end-use parts. Many of the plastic materials utilized in 3D printing today have qualities like those of conventionally produced plastics.
Especially for low to medium-scale production, this development enables businesses to incorporate 3D-printed plastic components straight into final goods. On-demand end-use part production helps to drastically lower lead times and inventory expenses.
Real-world testing of functional prototypes produced by 3D printing offers insightful information before major manufacturing commitments. In sectors like consumer electronics and automobiles, where dependability and product performance are vital, this capacity is especially valuable.
Conclusion
3D printing plastic offers several, broad benefits. From quick prototyping and affordable manufacturing to design freedom and supply chain adaptability, this technology keeps changing many different sectors. The possible uses and advantages of plastic 3D printing are probably going to grow much more as new materials are created and 3D printing technologies develop.
3D printing plastic is a great tool for invention and problem-solving as it allows one to produce sophisticated, customizable, and functional components with less waste and better efficiency. Unquestionably, this technology is transforming industry, healthcare, education, the creative sectors, and more. More companies and people using 3D printing plastic opens fresh design, production, and problem-solving opportunities that will shape manufacturing and beyond going forward.